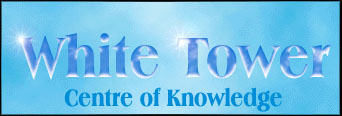
I'm writing this mainly for the folks on the Warhammer Fantasy mailing list. They've
answered a lot of questions for me, and even put up with my un-reasonable remarks
when I first joined. I'm hoping that I can return a little bit by sharing the knowlege I've
gained through experience. First off I'd like to thank Alvan Fisher Jr. whos article lead
me to believe that I too could do some casting. I'd reccomend reading his article as
background, and using my article as the "nuts and bolts" detailed description.
First let me declare that I am NOT an expert, and many steps of this process can be
dangerous and expensive. Please don't burn off your fingers, or poison yourself with
the chemicals. Your safety is up to you. I take no responsibility for your actions, so
think everything through carefully before each step.
With that out of the way, I estimate that you will be able to create molds for figures at
about $4 per figure for an average sized and shaped figure.
SUGGESTED MATERIALS
RTV Silicone rubber
Plasticene
A master figure you want to duplicate
Leggo building blocks
Rubber gloves
Plastic disposable cup
Popsicle stick (for stirring)
Petrolium Jelly
A small candle piece and knife
A very level surface
MATERIALS DISCUSSION
Ok, lets start with the basics. RTV stands for Room Temperature Vulcanizing. What
this means, is that the rubber comes in two liquid parts, that when mixed together and
allowed to cure at room temperature, they become a solid rubber. Later in the article I
will discuss the pros and cons of various type of RTV. However for our discussion they
are pretty much all the same.
Plasticene is a sulphur free clay. Since the RTV which we are using are mostly silicone
and tin based, we cannot have sulphur in the clay we are using. The sulphur reacts
with the chemicals in the RTV mixture and prevent them from curing (hardening) into a
solid. Plasticene is one of the least expensive and most important materials in the
entire process. Don't skip and try to use regular modeling clay, it's not worth it.
The master figure which you choose is important. It should have lots of pronounced
detail instead of lots of barely visible detail. Whenever you reproduce anything, by any
method, you are going to lose a slight amount of detail. It should also be un-painted
since the paint will probably obscure details in the molding process. Depending on the
paint, it could also interfere with the curing process of the RTV.
You should also keep in mind that the figure you are about to reproduce is probably
protected under copyright law. This means that the owner of the ORIGINAL figure has
the right to copy it, and you do not. Since I have no knowlege of copyright law,
pertaining to miniatures, I will tell you this much; "Unless you have sculpted the figure
yourself, copying figures is probably illegal". You are responsible for your own actions,
so if the copyright police knock on your door next thursday, you can't say that you
weren't warned.
Leggos make an ideal system for pouring the mold. You can create a perfectly square
mold in any size you like which is sturdy, yet will "break" apart to allow for easy mold
removal. If you do not have this luxury, try using small square paperboard boxes, such
as those that rings and jewlery come in. A square tough box is important to making a
good mold.
Since you and I do not know the chemical makeup of the RTV (and they aren't telling
since it's generally a trade secret) you should always wear rubber glove while working
with the chemicals.
THE MOLD MAKING PROCESS
For teaching purposes we shall discuss copying a commercial figure. Since this is
illegal, I'm sure that you will dutifully destroy both the mold and any copies you have
made as an upstanding citizen.
First look at the figure that you are going to cast. If it was cast to begin with, you should
be able to duplicate it. Look carefully at the figure and you will see the "flash" lines.
This is where the two halves of the mold came together. Next try to figure out which
direction the metal was poured from. Sometimes it will be poured from the base, and
other times, it will be poured from the head. Look at the figure in terms of "uphill" and
"downhill". First hold it with the base towards the floor, and imagine the figure as a
hollow shell designed to hold water. Now, if you were to pour water into that shell from
the head, would it fill up completely? If the water would have to flow "uphill" then it
won't fill (since gravity actually does work...). If it doesn't fill that way, try turning the
figure upside down, and pour from the base. A good hint is that almost anything with a
raised sword was probably poured from the base. GW figures are most likely poured
from the base.
Build up your leggo box such that both the figure and the sprew will fit into it with about
1/2 inch to spare on the three sides where the sprew is not going to be. Fill the bottom
of the box with plasticene. It should be at least as thick as 1/2 of the figures thickness
(including the base if any). If you make it too thick it will be ok, however of you make
it too thin, you will have problems.
After you have filled the bottom of the box, you may wish to level and smooth the
plasticene. Press on the figure until it is immersed in the plasticene up to the flash line.
Be careful that you do not bend small thin parts such as bows and swords. This is
particularly important for plastic minis since they will bend back to their original
shape and leave a hole in your mold. It has been suggested that applying a hair
drier (or other such heat) will soften the plasticene to allow for easier placement
of the model. If necessary, build up the plasticene so that the model is completely
encased up to the flash line of the original. Try to build up in large lumps, and not
in small thin layers. Thin layers have a tendency of folding over and stopping up the
metals flow.
Now that have settled the figure into the plasticene, create several "keys" by pushing a
dowel (or other such round object) into the plasticene in the large flat areas where the
figure will not be distrubed. Don't go too deep or you will have to use a lot of RTV to
cover them. Double check your figure to make sure that making the keys has not
disturbed its' placement.
What you have now done is created the bottom half of the mold in plasticene. So, place
the box on a level, chemical resistant surface (newspapers do just fine, but don't ruin
your best table by getting gook all over it.). When I say level, it's a good idea to drag out
a bubble level and check it. If it's off by just a little bit, it will be more difficult to pour. A
little extra time spent here will save you a lot of frustration later.
Now that your box is level, you can mix a small amount of the RTV according to the
directions using your plastic cup and popsicle stick. Once it has been mixed thoroughly,
pour the mixture over the top of the figure and fill the box to about 3/8 in thick, or to
completly cover the figure, whichever is greater. If you are pouring just one mold, you
might as well use it all, since it will set before you can use it anyway. Make sure that
you mix enough RTV to completely cover the figure. If you come back and find that it
has not completely covered the figure, you can mix more and pour it on even after it has
set. RTV will bond to itself without a release agent. Let this first half cure according to
the directions. I generally let it cure for 24 hours, but I've done as little as 12 with good
success, and some RTV's will cure faster with heat in even less time. Don't try to cure in
a cold environment, because it won't work.
After it has cured, break apart the leggo box and pull everything out. Next seperate the
plasticene and the RTV mold half. Attempt to leave the original in the RTV while removing
only the plasticene. If this is not possible, don't sweat it. It does not matter at this
point what happens to the plasticene, since we are finished with it until the next mold.
Now, place the first half of the RTV mold into the base of the leggo box and build it
back up. Put the master and sprew back into the RTV mold half. Make sure that the
model fits snugly into the RTV and that there are no gaps between the RTV and the
figure. If there are, you must do something to correct the problem. The most common
problem is the figure bending as you remove the plasticene. If this happens try to bend
it back into place. If this is not possible, you will have to fill this gap with petrolium jelly.
Unfortunately, this will make that particular area look much thicker than the original. For
swords and other thin objects (where it is most likely to occur) this can look really bad.
So don't fill it unless it is absolutely necessary.
Once you have refitted the figure and sprew into the mold, give all visible RVT a good
coating of petrolium jelly. This will prevent the second mold half from bonding with the
first half. You must put enough on it so that every part is visibly shiny, but not so much
that it is in clumps. If you were unable to fill in any small gaps between the figure and
the first mold half you must fill them now. I've only had to do this twice, so you probably
won't have to, but I'm telling you how to deal with it just in case.
Now that you've coated the RTV (and avoided the figure since that would hide some
detail) you can pour the second layer. Again it is important to completely cover the
figure and the RTV keys that are now sticking up. It's better to have it thicker than
thinner, and if you pour too little on, you can add more later, even after it has cured.
Once the second layer has cured completely, you can remove the mold from the box.
Remove the figure and carefully wipe all of the petrolium jelly from the
mold. If this is left on, it will burn and perhaps destroy your mold when molten metal is
poured into it. Next cut a sprew using an razorblade from the base of the figure to the edge
of the box. It might be advisable to cut several air-vents to allow air to escape.
You should let it continue to cure for 24 hours after seperating the halves. This will
insure the best life for your mold. Your mold will then be ready to use. You may use
either pewter, lead, or a casting resin in your new mold. I prefer pewter because it
provides the best detail in the shortest time. Lead has a higher melting temperature and
your mold may not last as long when using it. It can also cause brain damage if inhaled or
injested. Be very careful when using lead. Casting resin will not deteriorate your
mold, but takes time to cure, so doing 30 figures could take you as many days. In
addition, casting resin must be used with a shaker table to prevent bubbles from
forming.
There are lots of things that you can use to improve your molds. A vacume chamber
would prevent your molds from bubbling, as would (for exactly the opposite reasons) a
pressure chamber. A shaker table can provide the same benefit, however it might also
shake loose the figure from the mold half. I've had some success with pouring the mold
as one solid piece around a figure suspended from it's sprew, but you must then be very
careful in how you cut it, and you don't have keys to keep the mold pieces stable as you
are pouring. It is possible to buy "key cutters" however I feel that 2 piece molds are
better.
CASTING DIFFICULT FIGURES
- MOUNTS
To cast a four legged creature successfully, you must change the way you are
looking at molds. Instead of the mold being flat pieces, think of of as a wave
shaped object. The idea here is to bisect each leg, not the body. Below is a
ground up view of a horse. The lines are the part in the mold. The circles are the legs.
|=======================|
| |
| |
| |
|------O O--------|
| \ / |
| O---O |
| |
| |
|=======================|
UPHILL FLOWS
There are times that no matter how you orient a figure, it will make some
part of it become "uphill". You can aleviate this problem by making
additional channels for the metal to flow through by either cutting it out
of the rubber, or by placing an extra piece of wire as you create your mold.
The latter method works the best, but the former can be useful if you find
that some part is just not filling properly.
MATERIALS SOURCES
Below are different mold making suppliers. The prices have likely changed
so call first.
******PolTek Development Corp*******
* PolySil 70-25 So far the best I've tried, loses detail after each pour,
good figures for first 20-30. Supposed heat resistance of 300 F
Price $13.00/lbl $86.00/ 9 lbls
25 cubic inches/lbl
* PolySil 70-60 Better heat resistance than 70-25, but much more brittle.
Seems to lose detail faster even though higher heat resistance to 600 F.
Price $14.50/lbl $100.00/ 8.40 lbls
18 cubic inches/lbl
* PolySil 71-40 Havent tried it but since it is "non-shrinking" it will
probably give the best detail, and maybe shrink less. Heat resistance only
250 F.
Price $15.50/lbl $108.00/ 9 lbls
25 cubic inches/lbl
They sell plasticene and casting resins also.
1-610-559-8620 These guys are mostly into doing plastics. They give first
time discounts.
********Rio Grande Tools & Equipment *************
*701-014 High Temperature RTV mold compound. Supposedly designed to
withstand temperatures up to 1100 F, and advertised for pouring white metals
pieces. Says it must be vacuumned for best results. I haven't tried this
but sounds like a good replacement for PolySil 70-25. Much more expensive
but I believe that it will have a longer life span.
Price $36.50/lbl 206.21/ 8.8 lbls
24.61 cubic inches/lbl
*701-012 Ditto 3D. "Accepts molten metal up to 900 F" Again, haven't tried
it, but with better heat resistance, you'll get better detail from your 4th
and higher castings. It also advertises tear resistance, extra strength and
flexibility.
Price $41.00/lbl No price listed for economy kit
No mass/volume ratio given.
*750-003 American Casting Pewter Consists of 92%Sn 7 1/2% Sb 1/2% Cu.
Casting range 500-600 F. Sold in 4 lbl increments at $5.50/lbl.
1-800-545-6566 This company seems to specialize in jewlery, and lots of
lost wax style castings. If you order, ask for a catalog. Tons of stuff to
dool over, yet un-affordable...
*********************************************
Getting lead - I you prefer to use lead (for whatever reason) an exellent
source of lead is your nearby tire shop. Just ask them if you can
have/purchase their used tire weights. You can just drop them into your
crucible and the steel crimps will just float to the top. Pretty cool
effect to see steel float!
|